جی آر پی
لوله های GRP لوله های کامپوزیتی می باشند ک با توجه به توسعه فناوری های کامپوزیتی و نانوکامپوزیتی دارای قابلیت و کاربرد های مختلف جهت استفاده در زیر ساختها را فرراهم نموده اند.
امروزه فن آوری های جدید در روش های تولید لوله امکان کسب عملکرد بهتر با هزینه کمتر را فراهم نموده است. لوله های GRP دارای تکنولوژی برتردر مقایسه با دیگر لوله ها می باشند هم اکنون در پروژه های کلان در نقاط مختلف جهان به عنوان اولین گزینه مورد استفاده قرار میگیرند.
لوله های نوین کامپوزیتی جایگزین مناسبی برای انواع لوله ها مانند Ductil Iron . Cupper Nikel . Titanium alloy . Carbon steel . Stainless steel می باشند این لوله ها با مقاومت مکانیکی بسیار بالای اقتصادی نسبت به لوله های فلزی جایگزین بسیار مناسب برای مقابله با خوردگی در لوله های فلزی می باشند.
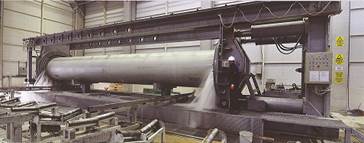
با توجه به اینکه این لوله هااز ترکیب الیاف فایبر گلاس و رزین با نسبت های خاص تشکیل یافته اند.تولیدکننده باانتخاب صحیح ترکیبات و مقدار موتدانتخاب فرایند مناسب میتواند به لوله با خصوصیات دلخواه دست یابد
انواع لوله ها:
1_ لوله های GRP
2_ لوله های GRVE
3_ لوله های پایپ جک جهت عملیات لوله رانی
4_ لوله های مقاوم در برابر سایش
5_ لوله های مقاوم در برابر حریق
6_ لوله های ویژه اتقال میعانات نفتی یا انواع سیالات آتش زا
7_ لوله های Uni Axial جهت مصارف دفنی
8_ لوله های Bi Axial لوله های شبه فولادی با مقاومت مکانیکی شبیه به لوله های فولادی و مقاوم در برابر انواع خوردگی های شیمیایی
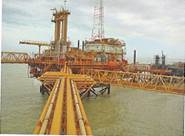
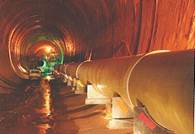
محدوده تولید :
قطر : 25 الی 4000
فشار : 1 الی 50 بار
سفتی : 2500 الی 20000 پاکسال
این محدوده تولید شامل انواع محصولات استانداردهای داخلی و بین المللی می باشد.
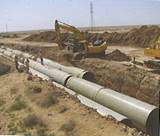
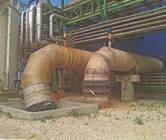
دامنه کاربرد :
علاوه بر اینکه محصولات کامپوزیتی دایره وسیعی را در صنایع پیشرفته مختلف از جمله هوا فضا . نفت . صنایع خودرو دارند و همچنین با توجه به مزایای مختلف اقتصادی . مقاومت خوب در برابر خوردگی . پایین بودن زبری سطح وثابت بودن آن در طول زمان و مقاومت مکانیکی بسیار بالای لوله های کامپوزیتی کاربردهای بسیار گسترده ای برای آنها وجود دارد
_ خطوط انتقال و توضیع آب ( آب خام و آشامیدنی)
_ شبکه های جمع آوری فاضلاب
_ شبکه های جمع آوری آبهای سطحی
_ خطوط انتقال سیالات شیمیایی
_ سیستمهای انتقال آب دریا
_ شبکه های آبیاری و زهکشی
_ پروژه های کنترل ورود و خروج آب در سدها
_ سیستم های آب خنک کننده
_ سیستم های اطفاء حریق
_ سیستم های لوله رانی بدون حفر ترانشه باز
_ خطوط انتقال انواع سیالات نفتی
_ خطوط انتقال انواع پساب های نفتی . صنعتی و شیمیایی
_ پروژه های نیروگاهی (Hydro Power Plant)
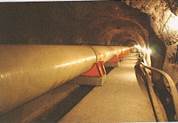
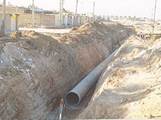
فرایند تولید لوله :
تولید لوله در اقطار 300 تا 4000 میلیمتر بر اساس فرایند پیشرفته الیاف پیچشی به روش پیوسته (contionuos filament winding) تولیدمیشود این فرایند امکان استفاده از الیاف پیوسته شیشه را در پیرامون لوله به همراه الیاف بریده شده (CHOP) که در جهات مختلف در ترکیب لوله قرار می گیرد فراهم آورد. بکارگیری الیاف پیوسته در این جهت علاوه بر کاهش هزینه تولید آن باعث افزایش استحکام لوله می گردد بنابراین لوله های تحت فشار مدفون فشار را در جهت حلقوی به خوبی تحمل خواهند کرد در این روش با استفاده از فن آوری کسب شده از متخصصان امر3 نوع مواد اولیه اصلی جهت ایجاد لایه ای فشرده با حداکثر کارآیی استفاده می شود علاوه بر رزین . الیاف شیشه ای پیوسته و الیاف بریده شده با هم برای ایجاد استحکام حلقوی بالا و تقویت استحکام محوری بکار میروند سیلیس نیز برای افزایش سفتی لوله بسته به کاربرد لوله میتواند استفاده شود.
در قطرهای زیر 300 میلیمتر موتد مورداستفاده مشابه تولید پیوسته است با این تفاوت که به روش نا پیوسته تولید انجام می گیرد.
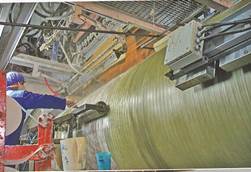
استانداردها :
استاندارد های API . ISO . DIN . Norsak جهت کاربردهای مختلف لوله از جمله انتقال آب آشامیدنی . جمع آوری فاضلابهای شهری . سیال ها و پساب های نفتی . پساب های صنعتی و مواد شیمیایی بکار گرفته می شود وجه مشخص استاندارهای مختلف تعریف کارآیی لوله ها برای مصارف خاص بر اساس عمر مفید می باشد.
استاندارهای ملی ایران
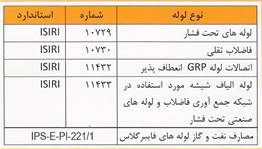
استاندارد ASTM :
در حال حاضر چندین استاندارد مختلف ASTM برای لوله جهت مصارف مختلف وجود دارد.استاندارد های مزبور شامل آزمونهای تاییدصلاحیت و تتهای کنترل کیفی است.

استاندارد ISO 14692 . APH 15 LR . API 15 HR :
استانداردهایی مانند ISO 14692 . APH 15 LR . API 15 HR برای برسی و گزینش لوله های فایبر گلاس مورد استفاده در صنعت نفت کاربرد دارد با استناد به این استانداردروش پیچش الیاف به عنوان یک فرایند توصیه شده برای ساخت این نوع لوله ها معرفی می گردد استانداردهای مربوط به آزمون های بلندمدت احراز صلاحیت نیز با جزئیات قید شده اند لوله ها مطابق با الزامات استاندارهای ذکر شده طراحی شده اند و در حال حاضر در سطح گسترده ای در واحدهای عملیاتی تابع وزارت نفت اعم ازپالایشگاه هاو پتروشیمی ها و سکوهای Offshore در حال بهره برداری می باشند.
استاندارد (CEN . TSEN ) ISO ,TSE :

استاندار ASME و AWWA :
AWWA C 950 یکی از جامع ترین استاندارها های تعریف شده برای لوله های GRP می باشد این استاندارد در کاربرد خطوط انتقال آب تحت فشار دارای مشخصات کامل برای لوله و اتصالات می باشد که براساس آزمایش های کنترل کیفیت و تعیین صلاحیت طبق الگوی مناسب طراحی شده است. AWWA راهنمای استاندارد طراحی را تحت نام M45 تدوین نموده ک چندین بخش آن به طراحی لوله های GRP در کاربردهای نصب مدفون و روی کار اختصاص یافته است.
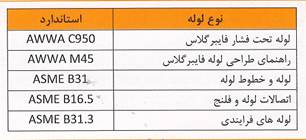
آزمون های کنترل کیفی :
از آنجا ک کیفیت مواد اولیه تاثیر عمده و اساسی در کیفیت تولیدات شرکت سازنده دارد لذا خرید این مواد با دقت و از منابع قابل اعتماد انجام شده و تستهاو آزمایشات لازم روی آنها پیش از مصرف به عمل می آید.بدین ترتیب کیفیت تولیدات مطابق استاندارهای شرکت و مشخصات فنی لوله تضمین خواهد گردید.علاوه بر آن آزمایشات کنترل کیفی مناسب بر روی مواد خریدلری شده در بدو ورود به کارخانه مطابق با برنامه کنترل کیفیت شرکت بعمل می آید.
کنترل کیفیت در سه مرحله انجام میگردد:
1_ آزمون های قبل از تولید به روی مواد ورودی
2_ آزمون ها و کنترل های حین تولید
3_ آزمون های پس از تولید به روی محصول نهایی
مواد اولیه اصلی در تولید لوله های GRP :
1_ الیاف شیشه
2_ رزین
3_ کاتالیست
4_ فیلر (ماسه سیلیسی)
5_ افزودنی های شیمیایی و شتاب دهنده ها
6_ سرفیس مت
لوله های تولیدی از مواد مورد بازبینی و اندازه گیری قرار میگیرد:
_ بازدید چشمی
_ سختی BARCOL
_ ضخامت جداره
_ طول شاخه قطر
_ آزمون هیدرااستاتیک ( تحت فشاری برابربا دو برابر فشاراسمی لوله ها)
_ آنالیز ساختار لوله ها و تادییدیه طراحی (L.O.I)
_ آزمون کشش در جهت محوری (شعاعی)
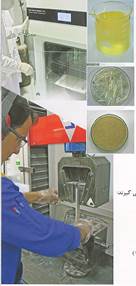
آزمون های احراز صلاحیت :
آزمون های صلاحیت سنجی آزمونهایی هستند ک منطبق با استاندارد بین المللی و همچنین استاندارد ملی ایران انجام آنها الزامی می باشد به این آزمون ها بلند مدت گفته میشودزیرا مدت زمان بیشتر این تست ها 10000 ساعت (حدود یکونیم سال) میباشد. آزمون های صلاحیت سنجی برای سه هدف عمده انجام میشود :
1_ تعیین مقاومت های مکانیکی بلند مدت مواد اولیه ای که درساختار لوله به کار می رود. توضیح اینکه مقاومت مکانیکی بلند مدت 50 ساله توسط تست های صلاحیت سنجیتعیین می گردد تست های کوتاه مدت وادهای کنترل کیفیت تاییدی بر تست های بلند مدت می باشد.
2_ به دست آوردن نتایج جهت طراحی لوله های GRP با طول عمر مفید 50 ساله
3_ انجام تست های مجدد صلاحیت سنجی جهت تایید اینکه تولید کنندگان مواد اولیه دارای فرمولاسیون و کیفیت ثابت می باشند.
مهمترین آزمون های صلاحیت سنجی:
_ Hydrostatic design basis
_ Long term ring bending strain
_ Long term specific ring stiffness
_ Long term strain corrosion
علاوه بر تست های بلند مدت تست هایی دیگری انجام می گیرد :
_ مقاومت در برابر اشعه
_ مقاومت در برابر سایش
_ تحمل دمایی بلند مدت برای دماهای بالا
_ مقاومت در برابر حریق
_ تست اتصالات ( بلند مدت و کوتاه مدت)
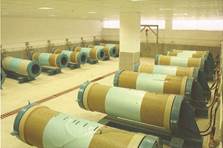
محدوده تولید
قطر :
لوله ها با قطر اسمی زیر تولید میشوند قطرهای کوچکتر یا غیر از قطر های اشاره شده نیز در صورت سفارش تولید می گردد
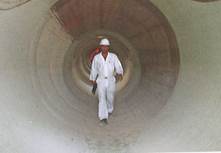
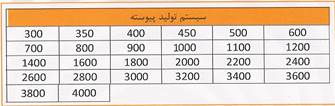

طول :
طول استاندارد لوله ها برای قطر های بزرگتر از 300 میلیمتر . 12 متری و برای قطرهای 100 تا 300 میلیمتر 6 متر و برای قطرهای زیر 100 به صورت 3 متری می باشد. البته در مصارف خاص امکان تولید با طول های دیگر نیز وجود دارد.
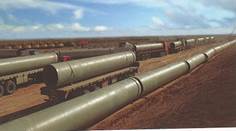
فشار :
کلاس های فشاری معمول لوله ها در جدول زیر فهرست شده اند.
فشار کاری لوله ها طبق استاندارد AWWA و در کتابچه طراحی لوله های فایبر گلاس محاسبه شده اند. رده بندی فشاری بر اساس حداکثر فشار در زمان کارکرد تعیین میشود و بستگی به عمق دفن لوله ندارد.
لوله ها تا قطر 4000 میلی متر و حداکثر فشار کاری 50 بار تولید می شونداین لوله ها به دلیل ساختار خود قابلیت طراحی جهت انواع سیالت با Hp های گوناگون(اسیدی یا بازی) را دارا هستند و دارای مقاومت بسیار بالا در برابر انواع خوردگی ها در محیط های شیمیایی می باشند.
هیدرو تست :

سفتی :
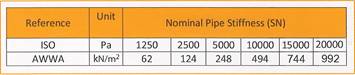
سرعت جریان :
سرعت محاز سیال درون لوله ها 3 متر در ثانیه است که این سرعت در صورت عدم حضور مواد ساینده درون سیال تا 9 متر در ثانیه قابل افزایش می باشد
ضریب پوآسون :
این ضریب وابسته به ساختار لوله میباشد. ضریب پوآسون در لوله ها برای بارهای حلقوی و عکس العمل محوری بین 24/0 تا 29/0 و برای بارهای محوری و عکس العمل حلقوی اندکی کمتر از مقدار فوق می باشد.
مقاومت در برابر اشعه UV :
حدود 5 درصداز نور خورشید را اشعه UV تشکیل می دهد که طول موج های 280 الی 400 نانومتر را در بر میگیرد. معمولا انرژی تابشی خورشید را با واحد لانگلی اندازه گیری می کنند.
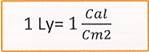
معدل تابش خورشید در کشورهای مختلف بر اساس کیلو لانگلی :
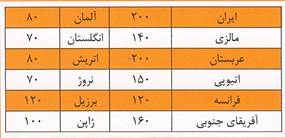
تحقیقات و آزمایش های نشان میدهد در صورتی ک انتخاب لوله ها به صورت صحیح انجام شده باشد اشعه U.V تاثیری بر لوله ندارد. به طور کلی لوله ها به دو نوع روی کار و دفنی تقسیم بندی می شوند. در لوله هایروی کار ترکیبات جاذب U.V (شیمیایی) و یا ترکیبات دافع U.V (فیزیکی) استفاده می گردد. اگر لوله های دفنی برای بیش از یک سال در محیط بیرونی و در معرض آفتاب قرار بگیرد توصیه می شود از مواد افزودنی مقاوم در برابر اشعه U.V استفاده گردد.
دمای کارکرد :
لوله ا قابلیت طراحی برای انتقال طراحی برای انتقال سیال تا دمای 160 درجه سانتیگراد را دارا می باشند. دمای مجاز سیال در لوله های استاندارد که در ترکیب آنها از رزین های پلی استری متداول استفاده گردیده است (بدون طبقه بندی رده فشار) حداکثر 45 درجه سانتیگراد میباشد. توصیه می شود ک برای کارکرد پیوسته در دمای بین 50 تا 60 درجه سانتی گراد رده فشاری یک رده بالاتر در نظر گرفته شود. مثلا برای فشار کاری 6 بار از لوله 10 بار استفاده شود. در دماهای بالتر از رزین های دیگر با مقاومت دمایی بیشتر و همچنین طراحی ویژه استفاده می گردد.
ضریب انبساط حرارتی :
ضریب انبساط و انقباض حرارتی لوله ها در جهت محوری در محدوده زیر می باشد
این ضریب در جهت محوری حدود 5/1 تا 2 برابر فولاد است. البته در طراحی و ساخت کوپلینگ ها در مارف زیر زمینی ضریب فوق مورد توجه قرار میگیرد بدین ترتیب ک انبساط و انقباض لوله در کوپلینگ جبرن می شود و در نتیجه تنشهای بوجود آمده به علت افزایش یا کاهش طول لوله حذف می گردد. درمصارف روی کاری ک اتصال لوله ها ب صورت صلب انجام می گیرد و تغییر طول لوله ها مهار نمی شود می بایست خطوط لوله تحلیل تنش شوند و در صورت نیاز استفاده از expansion loop یا expansion goint در این نوع اتصال ضروری است
ضریب هیدرولیکی :
افت فشار خطوط لوله بدلیل تغییر ارتفاع. اغتشاش جریان ناشی از تغییرات ناگهانی سطح مقطع در مسیر و اصطکاکی فشار در لوله بکار می رود.
روش های متداول شامل معادله Hazen Williams , Darcy- Weisbach,Manning می باشد. ضرایب ذیل در معادلات مربوطه طراحی به کار میروند
1_ در معادله hazen Williams : ضریب ضبری C برابر است با 150 الی 165
2_ در معادله manning : ضریب زبری برابر است با n= 0.009
3_ در معادله Darcy-weisbach : عدد زبری سطح برابر است با e=0/00518mm = surface roughness number
4_ در معادله Colebrook whit : ضریب k برابر است با k=0.029mm
از جمله مزایای این لوله ها نسبت به لوله های فلزی میتوان به پایین بودن زبری داخلی اشاره نمود. اثرات حاصل از این مزیت در سیستم های انتقال سیال تحت فشار بصورت های ذیل خواهد بود :
1_ کاهش میزان افت فشار (HF)
2_ کاهش هزینه برق مصرفی در ایستگاه پمپاژ (CP)
3_ افزایش ظرفیت عبور سیال (QP)
4_ کاهش قطر لوله مصرفی (D)
این موارد با استفاده از ردابط هیدرولیکی ( همانند رابطه هیزن – ویلیامز) قابل اثابت می باشد.
با توجه به اینکه نزدیک ترین قطر تولیدی لوله ها در سایز 1800 میلیمتر می باشد لذا می بایستی از لوله با قطر 1800 میلیمتر استفاده نمود. این در حالی است ک زبری داخلی لوله های فلزی با گذشت زمان افزایش می یابد لیکن زبری این لوله ها با گذشت زمان ثابت خواهد بود

مقاوت در برابر سایش :
این لوله ها در مقابل سایش مقاوم می باشند. ضریب مقاومت ساییدگی میتواند تاثیر شن و ذرات دیگر شبیه به آن را در سطح داخلی لوله پیش بینی کند. سایش این لوله ها به وسیله روش DARMSTADT ROCKER برسی شده اند. براساس آزمایش های انجام شده در دانشگاه DARMSTADT ساییدگی میانگین این لوله ها در برابر شن سیلیسی 34/. میلیمتر در 100000 دوران کامل می باشد.
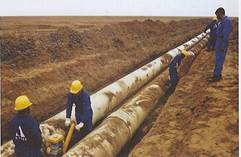
اتصال نو و مادگی :
این روش اتصال به طور معمول برای لوله های زیر 300 میلیمتر (12 اینچ) استفاده می شود. لوله های خاص برای اتصال با این روش در انتها دارای یک بر آمدگی هستند و ابتدا لوله پس ازاعمال رزین به دور آن در این قسمت برآمده فرو رفته وپس از خشک شدن یک اتصال صلب را ایجاد می کند.
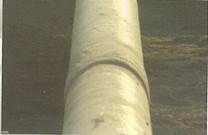
اتصال آداپتوری :
این روش یک اتصال صلب بوده که به کمک یک قطعه واسط به نام آداپتور اجرا می گردد. این روش اتصال در نصب لوله های روی کار به ویژه سکوهای نفتی و یا نصب دفنی استفاده می شود.
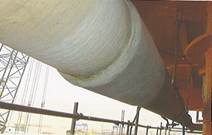
اتصالات جوشی یا لایه گذاری :
این اتصال از انواع مختلف لایه ها فایبر گلاس و رزین انجام می پذیرد طول و ضخامت اتصال بر اساس قطر و فشار کاری لوله تعیین می گردد. این نوع اتصال نیاز به پرسنل آموزش دیده و شرایط مناسب دارد.
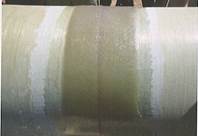
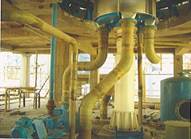
کوپلینگ چسبی :
کوبلینگ صلب با چسب اپوکسی جهت مصارف روی کار یا دفنی تامین می گردد. هنگامی از این نوع اتصال استفاده می گردد که نیاز به تامین مقاومت در جهت محوری لوله باشد. در این کوپلینگ ها آب بندی با دو واشر و چسب اپوکسی انجام می گردد ضمن ایمکه چسب اپوکسی بین لوله و کوپلینگ موجب صلب شدن کوپلینگ می گردد و در نتیجه اتصال مربوط کاملا مقاوم در برابر نیروهای کششی در طول خط می باشد
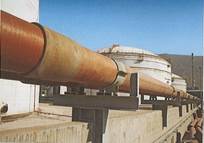
گوپلینگ رکا (مانشن) :
متداول ترین روش اتصال خصوصا برای لوله های مدفون استفاده از کوپلینگ رکا می باشد لوله های تولیدی در شاخه های 12 متری معمولا به وسیله یک پولینگ 2 واشره از جنس GRP به هم متصل می شود. لوله و کوپلینگ میتواند به صورت مجزا تامین گردد ولی معمولا در یک طرف بر روی لوله در کارخانه نصب خواهد شد. کوپلینگ های تولیدی با دو واشر آب بندی می شوند واشر درون شیاری که با دقت تراشکاری شده است قرار میگیرد واشر کوپلینگ ها برای مدت بیش از 75 سال مقاومند.
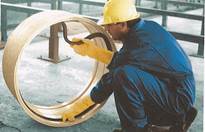
انحراف زاویه ای در محل اتصال :
اتصالات کوپلینگی طبق استاندارد ISO DIS 8639 , ASTM D 4161 تحت آزمون های متعددی قرار میگیرند.
اگر فشار اسمی لوله ها بیش از 16 بار باشد :
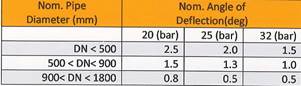
فلنج GRP :
در موارد خاص امکان اتصال فلنجی لوله ها وجود دارد وقتی که دو فلنج GRP در اقطار بیش از 300 میلیمتر به هم متصل می شوند پیشنهاد می گردد که یک فلنج در Face دارای O-ring باشد استاندارد سوراخکاری متداول به شرح زیر می باشد.
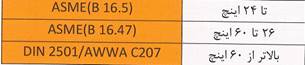
کلیه اتصالات :
کلیه اتصالات از جنس GRP از قبیل زانو در زوایای مختلف. سه راهی . فلنج . نازل در اندازه های استاندارد.
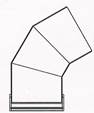
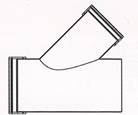
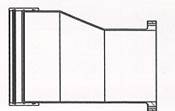
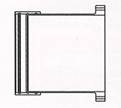
لوله های شبه فولادی ( دو محوره یا Bi Axal ) :
مشخصات فیزیکی :
طراحی لوله های Bi Axial ب گونه ای است ک می توانند مقاومت بسیار بالایی در جهت محوری و همچنین در جهت شعاعی داشته باشند. بنا براین این گونه لوله ها بسیار مقاوم تر از لوله های دفنی استاندارد می باشند. جهت نصب این لوله ها میتوان از روش های مختلف نصب همانند لایه گذاری یا کوپلینگ چسبی استفاده نمود
ملاحظات تحلیل تنش :
در لوله های روی کار به منظور ایجاد تحمل در برابر نیروهای محوری و شعاعی از سیستم اتصال صلب استفاده می شود (همانند اتصالات چسبی یا جوشی) ضریب انبساط حرارتی GRP تقریبا 2 برابر فولاد می باشد اما مدول الاستیسیته GRP کمتر از فولاد می باشد بنابراین تا حدودی نیرو کاهش می یابد برای این منظور می توان از سیستم های Expansion loop یا Expansion goint استفاده کرددر سیستم های دفنی در محل زانو ها در صورت نیاز از سیستم های Thrust block یا Anchor block یا فقط یک پشت بند ساده استفاده می گردد که بسته به نوع لوله تعیین میشود
فشار گذرا – ضربه قوچ :
شوک های داخلی ک شناخته ترین آنها ضربه قوچ می باشد در اثر تغییر ناگهانی در سرعت سیال درون سیستم ایجاد میشود که علت عمومی آن معمولا بستن و باز کردن شیر ها و یا شروع ناگهانی یا قطع پمپ های فشار می باشد. مدول الاستیسیته کم در لوله های GRP در قیاس با لوله های فلزی باعث توانایی بالا در دفع نیروی حاصل از موج در سیستم می شود.لوله ها در رده فشاری مختلف قادر تحمل ضربه قوچ تا 40 % بیش از فشار اسمی لوله می باشد رابطه تقریبی ذیل برای تعیین تغییرات فشار در نقطه های معین در خط لوله مستقیم با صرف نظر کردن از افت اندک ناشی از اصطکاک استفاده میشود.
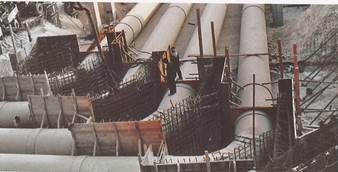
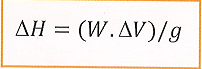




کاربرد های خاص
سیستم های لوله رانی بدون ترانشه باز:
در شرایطی ک امکان ایجاد ترانشه باز نباشد میتوان از سیستم لوله رانی (Pipe gacking) استفاده نمود. این لوله ها به صورت سیستم های تحت فشارنیز تولید می باشد. در مواردی نیز میتوان از این سیستم ها جهت ایجاد یک خط لوله جدید درون لوله قدیمی آسیب دیده استفاده نمود.
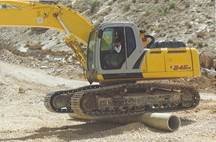
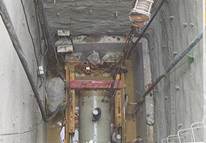
کاربردهای صنعتی :
شرکت سازنده دارای محصولات ویژه ای جهت استفاده در صنایع مختلف از جمله صنایع شیمیایی جهت انتقال انواع سیالات شیمیایی در دماهای مختلف و یا سیستم های مقاوم در بابر حریق ویا سیستم های مقاوم در برابر سایش می باشد.
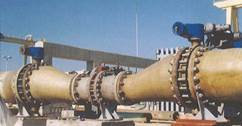
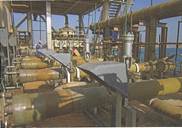
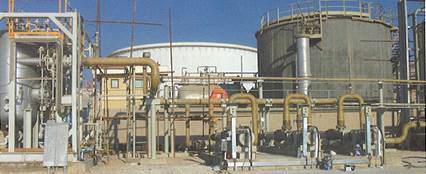